Die digitale Transformation der deutschen Industrie schreitet voran: Einer Bitkom-Studie aus dem Jahr 2022 zufolge nutzen oder planen 90 % der Unternehmen Anwendungen im Bereich Industrie 4.0. Besonders große Unternehmen sind hier Vorreiter, während kleinere Betriebe oft noch Nachholbedarf haben. Technologien wie Künstliche Intelligenz (KI), das Internet der Dinge (IoT) und digitale Zwillinge gewinnen zunehmend an Bedeutung und eröffnen neue Potenziale für Effizienz und Nachhaltigkeit. Dennoch sehen sich fast zwei Drittel der Unternehmen mit weniger als 500 Mitarbeitenden als Nachzügler in diesem Bereich, was auf dringenden Handlungsbedarf hinweist. In diesem Blogartikel erfährst Du alles rund um die Industrie 4.0 – über die aktuellen technologischen Trends, die Chancen und Risiken. Doch vorher klären wir erst einmal etwas Grundsätzliches:
Definition und Merkmale: Was versteht man unter Industrie 4.0?
Einfach erklärt, beschreibt die Industrie 4.0 ganz allgemein einen Innovations- und Transformationsprozess innerhalb der produzierenden Industrie. Ziel des Prozesses ist es, die reale mit der virtuellen Welt zu verschmelzen. Mittels modernster, digitaler Informations- und Kommunikationstechnik soll so eine intelligente Vernetzung zwischen Menschen, Maschinen und industriellen Prozessen geschaffen werden.
Neue Perspektiven für Unternehmen durch Industrie 4.0
Egal ob Großkonzern, Mittelständler oder Kleinunternehmen, die Industrie 4.0 bietet enorme Potenziale. So eröffnet die Digitalisierung Industrie 4.0 nicht nur neue Perspektiven für Beschäftigte, sondern auch neue Organisations- und Steuerungsmöglichkeiten für die gesamte Wertschöpfungskette. Dabei stellen innovative Formen des Wirtschaftens und Arbeitens die Leitplanken für die intelligente Verknüpfung von den bereits zuvor genannten Faktoren Mensch, Maschine und Prozess dar.
Digitalisierung und Vernetzung mit IT-Sicherheit umsetzen
Eines der weltweit führenden Netzwerke der Industrie 4.0 ist die Plattform Industrie 4.0. Neben gezielten Handlungsempfehlungen für Unternehmen, Wissenschaft und Politik entwickeln die Teilnehmer:innen der Plattform Industrie 4.0 Pläne, wie die Digitalisierung und Vernetzung unter den Standards der IT-Sicherheit zukünftig umgesetzt werden können. Darüber hinaus unterstützt die Plattform insbesondere kleine und mittelständische Unternehmen dabei, die Herausforderungen der Industrie 4.0 zu bewältigen.
Die industrielle Revolution: In 4 Schritten zur Industrie 4.0
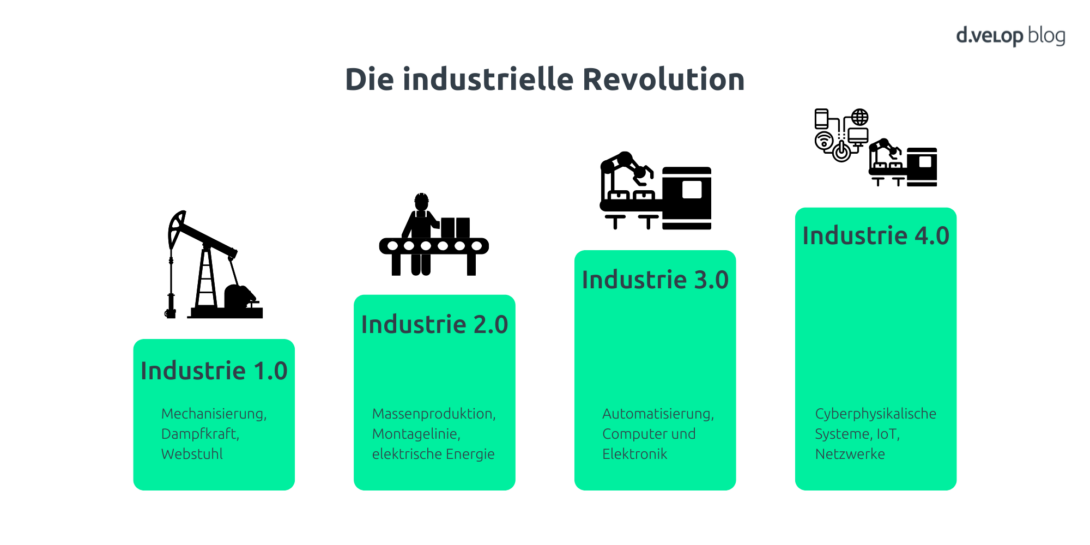
Dass Maschine heute miteinander über das Internet kommunizieren und automatisiert komplexe Prozesse abarbeiten können, ist kein Zufall. Seit jeher versuchen Menschen, sich die Arbeit durch Werkzeuge zu vereinfachen und so Prozesse zu verbessern und effizienter zu gestalten. In der Industrie ging dies in vier Schritten vonstatten. Hier ein Überblick über die Evolution der industriellen Revolution bis hin zur Industrie 4.0, wie wir sie heute kennen:
- Industrie 1.0 (Ende 18. Jh.) – Mit der Erfindung der Dampfmaschine begann die Mechanisierung der Produktion, wodurch manuelle Arbeit durch Maschinen ersetzt wurde. Dies legte den Grundstein für moderne Produktionsprozesse und Fabriken.
- Industrie 2.0 (Anfang 20. Jh.) – Die Einführung der Montagelinie und Elektrifizierung revolutionierte die Massenproduktion, wodurch Effizienz und Skalierbarkeit enorm stiegen. Durch Kommunikations- und Informationstechnologie verbesserten sich zudem Steuerung und Management der Produktion.
- Industrie 3.0 (1970er Jahre) – Automatisierung durch Elektronik, IT und erste Roboter optimierte Produktionsabläufe. Digitale Steuerungssysteme und Robotik steigerten die Effizienz und Präzision erheblich.
- Industrie 4.0 (heute) – Seit Ende des 20. Jahrhunderts wuchs die Bedeutung des Internets als zentrale Technologie in der Industrie. Seit 2011 steht der Begriff „Industrie 4.0“ für die zunehmende Digitalisierung und Vernetzung. Maßgeblich geprägt wird die Digitalisierung 4.0 in der Industrie durch das Internet der Dinge (IoT) und damit intelligente Technologien wie die künstliche Intelligenz. ² Vernetzte Maschinen, Maschinelles Lernen (ML) und der Digitale Zwilling ermöglichen eine intelligente, selbstoptimierende Produktion. Diese Digitalisierung Industrie 4.0 bietet neue Chancen und Risiken, da sie Prozesse flexibler und effizienter macht, aber auch Herausforderungen in Management und IT-Sicherheit mit sich bringt.
Beispiele für Chancen und Risiken von Industrie 4.0
Die Digitalisierung und die Industrie 4.0 bieten weitreichenden Chancen und Herausforderungen für Unternehmen. Diese zeigen, dass ein vorausschauendes Management entscheidend ist, um den Wandel hin zur Industrie 4.0 erfolgreich zu gestalten:
Chancen der Industrie 4.0
- Effizienz- und Produktivitätssteigerungen: Durch Automatisierung und digitale Vernetzung können Produktionsprozesse optimiert und schneller durchgeführt werden.
- Senkung der Kosten: Automatisierte Prozesse und optimierte Ressourcennutzung reduzieren Betriebskosten langfristig.
- Aktive Ressourcenschonung, um diese in anderen Bereichen zu investieren: Durch intelligente Systeme werden Materialien und Energie effizienter genutzt, wodurch Einsparungen für Innovationen freiwerden.
- Vollständig transparente Prozesse: Echtzeit-Daten ermöglichen eine lückenlose Nachverfolgbarkeit und Kontrolle entlang der gesamten Wertschöpfungskette.
- Schnelle, flexible Reaktion auf Marktveränderungen: Vernetzte Systeme und KI-gestützte Analysen erlauben eine agile Anpassung an veränderte Kundenbedürfnisse und Marktbedingungen.
- Maschinen können autonom auf sich ändernde Anforderungen reagieren: Durch Machine Learning und intelligente Sensoren können Produktionsanlagen sich selbstständig anpassen.
- Durch das Sammeln und Analysieren von Daten können neue Lösungen entwickelt und Arbeitsprozesse optimiert werden: Big Data und KI helfen, Muster zu erkennen und innovative Geschäftsmodelle zu entwickeln.
- Neue Arbeitsmodelle für Mitarbeiter:innen: Digitalisierung ermöglicht Homeoffice, flexiblere Arbeitszeiten und standortunabhängige Zusammenarbeit.
- Unterstützung durch vollständige Informationsbeschaffung und Entlastung von älteren Mitarbeiter:innen durch beispielsweise Lastenroboter: Smarte Assistenzsysteme erleichtern körperlich belastende Tätigkeiten und verbessern den Wissenstransfer.
- Verbesserung der Work-Life-Balance und Steigerung der Zufriedenheit der Mitarbeiter:innen durch die flexible Anpassung von Arbeitsabläufen: Automatisierung kann monotone Aufgaben übernehmen und Mitarbeitern mehr Freiraum für kreative Tätigkeiten bieten.
- Neue Wachstumschancen und Wettbewerbsvorteile für den Wirtschaftsstandort Deutschland: Technologische Innovationen und Digitalisierung stärken die globale Wettbewerbsfähigkeit deutscher Unternehmen.
- Flexible Produktionsumgebungen: Modular aufgebaute und vernetzte Fertigungslinien ermöglichen eine schnelle Anpassung an individuelle Kundenwünsche.
Risiken der Industrie 4.0
- Erhöhte Anforderungen an die IT-Sicherheit durch große Datenmengen zum Schutz vor Datenmissbrauch: Unternehmen müssen in robuste Sicherheitslösungen investieren, um Cyberangriffe und Datenlecks zu verhindern.
- Eingeschränkte gesellschaftliche Akzeptanz durch beispielsweise neue Arbeitsmodelle (Fokus auf Wissensarbeit statt körperlichen Tätigkeiten): Die Transformation von klassischen Arbeitsplätzen zu digitalen Berufen kann zu Widerstand und Unsicherheit in der Bevölkerung führen.
- Steigender Fachkräftemangel, beispielsweise an IT-Expert:innen durch veränderte Anforderungen an Mitarbeiter:innen: Die zunehmende Digitalisierung erfordert spezialisierte Fachkräfte, deren Ausbildung und Verfügbarkeit derzeit nicht ausreichend sind.
Digitalisierung Industrie 4.0: So steigern Unternehmen ihre Effizienz
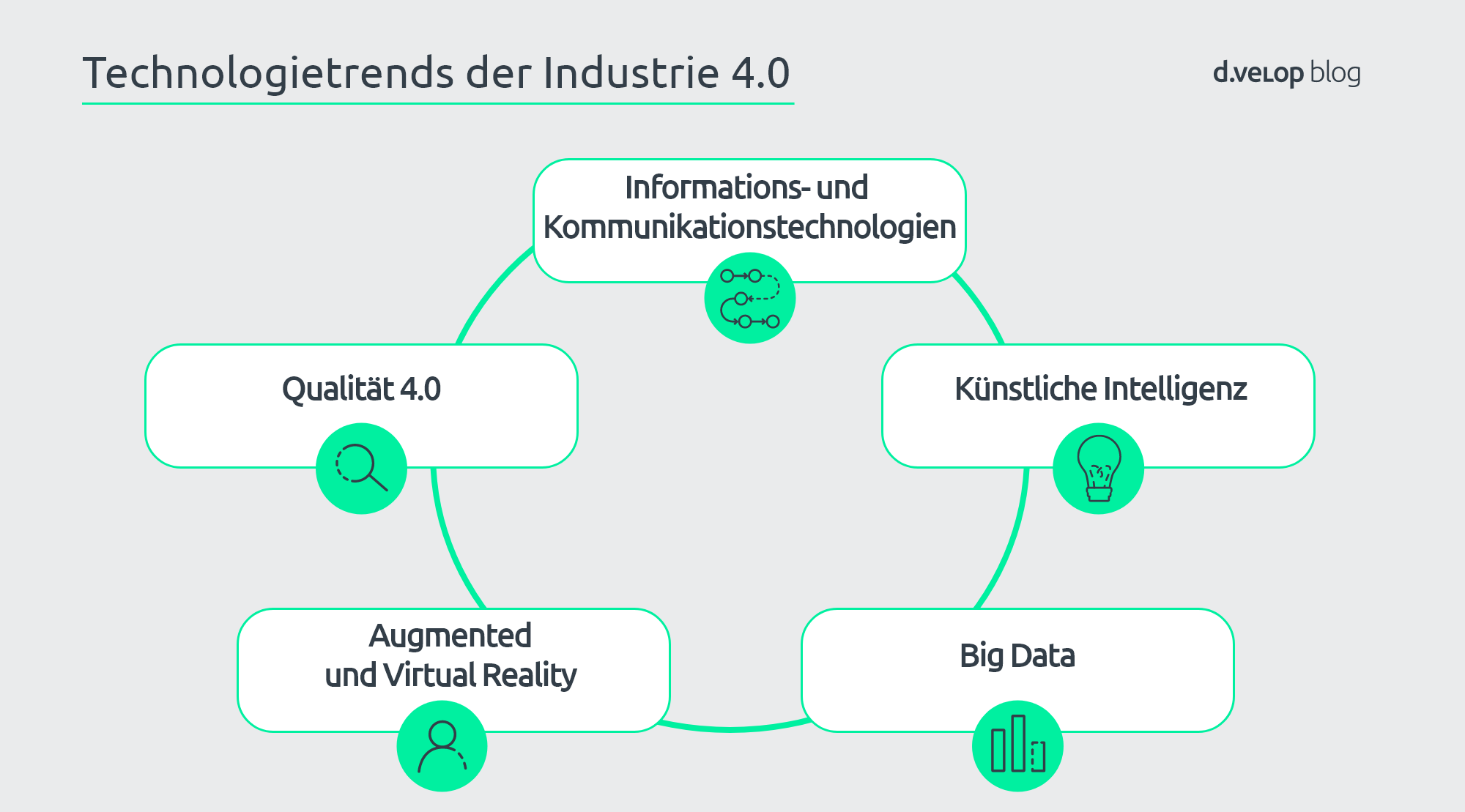
Den Startschuss für die Industrie 4.0 markiert das Internet der Dinge (IoT). Die intelligente Vernetzung von Maschinen ermöglicht vollumfängliche Automatisierungen wie die Wartung von Maschinen, die diese heutzutage selbstständig ausführen. Der menschliche Zugriff auf eine Maschine ist so nur im Ausnahmefall erforderlich. Durch die drahtlose Verbindung der Maschinen mit dem Internet können diese Informationen eigenständig erfassen, analysieren, verknüpfen und mit anderen Maschinen teilen.
Wichtige Technologien und Konzepte
Ob neue Technologien der künstlichen Intelligenz, Augmented Reality und Virtual Reality oder Big Data – Software, die Industrie 4.0-Prozesse unterstützt, bietet Industrieunternehmen enorme Vorteile bei der Herstellung von Produkten und Dienstleistungen. Beispiele für wichtige Technologien in Bezug auf Industrie 4.0 sind:
1. Informations- und Kommunikationstechnologien als Grundlagen
Sie stellen eine zentrale Rolle für die Industrie 4.0 dar. Ohne eine leistungsstarke Kommunikationstechnik ist eine effiziente Fertigung schlichtweg nicht möglich. Das gilt für drahtlose Datenübertragungen, etwa zur Vernetzung von Maschinen in der Produktion, wie auch für den Einsatz von VR.
2. Künstliche Intelligenz vereinfacht Arbeitsschritte
Eine effiziente Produktion ist in jedem Industrieunternehmen wichtig. Die künstliche Intelligenz setzt hier gezielt an, indem Maschinen durch moderne Technologien der Industrie 4.0 lernen, sich eigenständig funktional weiterzuentwickeln. So sind sie in der Lage, beim Verrichten von Arbeitsschritten bessere Leistungen erbringen. KI ermöglicht damit maschinelles Lernen und damit verbundene, kontinuierliche Produktverbesserungen, und das Entstehen neuer Geschäftsmodelle.
3. Gezieltere Handlungsentscheidungen mit Big Data
Die Datenmengen im Unternehmen wachsen immer weiter. Die Digitalisierung und die Industrie 4.0 sind dafür verantwortlich. Genau das beschreibt Big Data. Durch die Analyse dieser großen Datenmengen können Unternehmen viele nützliche Informationen gewinnen. Mithilfe intelligenter, selbst lernender Algorithmen lassen sich Verknüpfungen zwischen einzelnen Daten herstellen. So treffen Industrieunternehmen aufgrund besser prognostizierter Daten zielgerichtetere Entscheidungen und nutzen Wissen gezielter. ³
4. Die vielfältigen Möglichkeiten durch AR und VR entdecken
Computergestützte Modelle wie VR bieten Kunden ein ganz neues Kauferlebnis. Sei es der virtuelle Rundgang durch die Produktion oder das Erleben eines neuen Produkts. Die modernen Technologien der Industrie 4.0 können darüber hinaus Arbeitsschritte vereinfachen und effizienter gestalten. Per Smartphone oder Tablet lassen sich ganz einfach Informationen über Lagerbestände einsehen. So kann beispielsweise der Prozess einer Ersatzteilanfrage im Rahmen einer Maschinenwartung durch den Einsatz von AR beschleunigt werden. ⁴
5. Qualität 4.0
Ungenutztes Potenzial in der Produktion entdecken? Durch das Qualitätsmanagement in der Industrie 4.0 optimieren Unternehmen mithilfe neuster Technologien die Qualität ihrer gesamten Wertschöpfungskette. Dabei ermöglichen KI und Big Data umfangreiche Qualitätsanalysen. Mittels modernster Industrie 4.0-Software reagieren Unternehmen kurzfristig auf mögliche Fehler oderidentifizieren Engpässe.
Praxis-Beispiele: Wie Unternehmen Industrie 4.0 nutzen
Die folgenden Beispiele zeigen, wie sich Unternehmen verschiedener Branchen die Industrie 4.0 zunutze machen. Vernetzung, Automatisierung und Echtzeit-Datenanalyse spielen dabei eine zentrale Rolle:
Produktion 4.0 – Die Zukunft der Fertigung
Die Industrie 4.0 revolutioniert die Fertigung durch den Einsatz modernster Technologien wie Künstliche Intelligenz (KI), Internet of Things (IoT) und smarte Automatisierung. Unternehmen der produzierenden Industrie profitieren von kundenindividuellen Produkten zum Preis von Massenware – und das bei höchster Qualität. Digitale Zwillinge und vorausschauende Wartung (Predictive Maintenance) sorgen für kürzere Produktionszyklen und eine selbstständige Maschinenreparatur. Maschinenbau, Logistik und Dienstleistungen sind bereits heute vernetzt und kommunizieren autonom miteinander, um Prozesse effizienter zu gestalten. Die dynamische Produktion ermöglicht eine schnelle Anpassung an Marktveränderungen und steigert die Wettbewerbsfähigkeit.
Industrie 4.0 in der Automobilindustrie – Trend zur Individualisierung
Daten sind das neue Gold – insbesondere in der Automobilbranche, wo Fahrzeug- und Kundendaten zentrale Erfolgsfaktoren sind. Industrie 4.0 ermöglicht eine intelligente Vernetzung dieser Daten, sodass Hersteller auf personalisierte Fahrzeuge und maßgeschneiderte Services setzen. Unternehmen, die zuvor auf reine Preispolitik fokussiert waren, orientieren sich zunehmend an der individualisierten Massenproduktion. Zentral für diesen Wandel ist die Mensch-Maschine-Kollaboration: Während Service-Roboter schwere oder gefährliche Aufgaben übernehmen, behalten Menschen dank ihrer kognitiven Fähigkeiten die Steuerung und Kontrolle. Bereits 20 % der Automobilunternehmen nutzen selbststeuernde Anlagen in der Produktion – ein Trend, der weiter wächst.
Maschinenbau 4.0 – Automatisierung durch Cobots
Industrie 4.0 ist längst ein fester Bestandteil der Unternehmensstrategie großer Maschinenbauunternehmen. Digitale Technologien wie autonome Transportsysteme, vernetzte Logistiklösungen und Predictive Maintenance steigern die Effizienz und senken Kosten. Besonders im Fokus stehen kollaborative Roboter (Cobots), die Mitarbeiter:innen bei körperlich belastenden Aufgaben unterstützen. Ergänzend kommen smarte Technologien wie Datenbrillen, 3D-Druck und Software-Bots zum Einsatz, die Arbeitsprozesse automatisieren und optimieren. Diese digitale Transformation ermöglicht eine flexiblere Produktion, erhöht die Sicherheit am Arbeitsplatz und verbessert die Ressourcennutzung.
Industrie 4.0 in der Chemiebranche – Digitaler Fortschritt ohne Grenzen
Die Chemieindustrie gehört zu den größten Anwendern von Digitalisierungstechnologien, da sie unter starkem internationalem Wettbewerbsdruck steht. Industrie 4.0 eröffnet hier nahezu unbegrenzte Möglichkeiten: Smarte Sensoren überwachen die Produktqualität in Echtzeit, während KI-gestützte Systeme Rohstoffe effizienter einsetzen. Besonders in der Agrarbranche profitieren Landwirte von digitalen Lösungen wie präziser Düngemittelausbringung oder automatisierter Bodenanalyse. Durch die enge Zusammenarbeit zwischen Chemieunternehmen und Landwirtschaft entstehen nachhaltige, ressourcenschonende Lösungen, die Effizienz und Umweltfreundlichkeit vereinen. Im nächsten Abschnitt beleuchten wir, wie Landwirtschaft 4.0 die Agrarbranche transformiert.
Landwirtschaft 4.0 – Smarte Technologien für eine nachhaltige Zukunft
Effizienzsteigerung, Nachhaltigkeit und Digitalisierung prägen die Zukunft der Landwirtschaft. Technologien wie Big Data, KI, Agrar-Apps und autonome Maschinen ermöglichen Landwirt:innen eine präzisere und ressourcenschonendere Bewirtschaftung. Selbstfahrende Erntemaschinen, Drohnen zur Felderüberwachung und intelligente Bewässerungssysteme steigern nicht nur die Produktivität, sondern entlasten auch körperlich arbeitende Fachkräfte. Ein Hindernis bleibt jedoch die oft mangelnde Netzabdeckung in ländlichen Regionen. Trotzdem eröffnet Landwirtschaft 4.0 enorme Chancen für eine nachhaltige, technologiebasierte Agrarwirtschaft, die den steigenden Anforderungen der Lebensmittelproduktion gerecht wird.
Logistik 4.0 – Effizienz durch smarte Vernetzung
Eine vernetzte, digital gesteuerte Logistik ist das Rückgrat der Industrie 4.0. Logistik 4.0 nutzt Echtzeit-Daten für kürzere Lieferzeiten, optimierte Bedarfsplanungen und höhere Transparenz entlang der Lieferkette. Technologien wie GPS, Sensorik, Barcodes und KI ermöglichen eine nahtlose Integration aller Transport- und Lagerprozesse. Selbstfahrende Transportfahrzeuge und intelligente Güter, die eigenständig Transportplätze buchen oder Lagerbestände verwalten, revolutionieren die gesamte Wertschöpfungskette. So wird Logistik 4.0 zum entscheidenden Wettbewerbsfaktor in einer zunehmend digitalisierten Wirtschaft.
Erhalten Sie jetzt einen Einblick in die Software! 💻
Ist Industrie 4.0 noch aktuell?
Industrie 4.0 ist weiterhin aktuell, da viele Unternehmen noch mitten in der digitalen Transformation stecken und Technologien wie IoT, KI und Automatisierung implementieren. Allerdings gewinnt Industrie 5.0 an Bedeutung, insbesondere seit der EU-Kommission 2021 eine Denkschrift veröffentlichte, die den Menschen stärker in den Mittelpunkt stellt.
Industrie 5.0: Nachhaltigkeit, Resilienz, Mensch-Maschine-Interaktion
Während Industrie 4.0 auf Vernetzung, Effizienz und Automatisierung setzt, ergänzt Industrie 5.0 diese Konzepte durch Nachhaltigkeit, Resilienz und eine stärkere Mensch-Maschine-Interaktion. Industrie 4.0 fokussiert sich auf die Optimierung von Produktionsprozessen, während Industrie 5.0 darauf abzielt, soziale und ökologische Aspekte stärker zu berücksichtigen. Beide Konzepte existieren parallel, wobei Industrie 5.0 eine Weiterentwicklung und nicht eine Ablösung von Industrie 4.0 darstellt.
Stimmen: „Ich bin schon bei Industrie 9.0“
Auch in Foren des Internets wie Reddit wird viel über unterschiedliche Aspekte rund um das Thema „Industrie 5.0“ diskutiert. Wir stellen einige Positionen unkommentiert gegenüber, um die Vielfalt der Standpunkte zu dokumentieren:
- „Bedeutungsloses Buzzword 5.0.“ – Ein Nutzer hält Industrie 5.0 für einen bloßen Modebegriff.
- „AI für das Training von Vision-Systemen wird ein großer Gewinn sein.“ – Andere sehen in KI nützliche Anwendungen, insbesondere in der Bildverarbeitung.
- „Bei KI und Industrie 5.0 geht nicht darum, Wartungsteams zu ersetzen, sondern diese besser zu machen.“ – Ein Nutzer verdeutlicht, dass KI nicht auf den Ersatz von Arbeiter:innen abzielt, sondern auf die Verbesserung von Prozessen
- „Ich bin schon bei Industrie 9.0.“ – Ein humorvoller Kommentar, der die oft überzogene Weiterentwicklung solcher Konzepte kritisiert.
- „Die Integration von Mensch und Maschine macht die Industrie wieder menschlicher.“ – Ein User glaubt, dass Industrie 5.0 die Interaktion zwischen Menschen und Technologie betont.
- „Es geht nicht nur um Effizienz, sondern auch um nachhaltige Entwicklung.“ – Dieser Nutzer legt den Fokus von Industrie 5.0 auf Umwelt und sozial verantwortungsvolle Innovationen.
- „Die Herausforderung liegt in der Umsetzung in großen Unternehmen“ – Ein anderer Nutzer warnt vor praktischen Schwierigkeiten, die größere Firmen bei der Einführung von Industrie 5.0 haben könnten.
Der Startschuss zur Industrie 4.0 ist gefallen
Industrie 4.0 ist schon lange keine Zukunftsmusik mehr. Die vierte industrielle Revolution hat längst begonnen. Nutze die Möglichkeit, Prozesse effizienter zu gestalten. Das kostenfreie Webinar „In 30 Minuten zum digitalen Aktenplan für die Industrie“ gibt einen Einblick, wie sich umfangreiche Projekte mit zahlreichen Dokumenten ab sofort übersichtlich darstellen lassen. Anschauen lohnt sich!
Digitale Akten: So gelingt die Einführung – inklusive 7 Erfolgsstories
Häufige Fragen zu Industrie 4.0
Für Industrie 4.0 braucht dein Unternehmen eine vernetzte IT-Infrastruktur mit smarten Sensoren, Cloud-Plattformen und KI-Technologien wie Maschinelles Lernen, um Produktionsprozesse effizient zu steuern. Durch digitale Zwillinge, Robotik und moderne Kommunikations- und Informationstechnologien kannst du Chancen wie höhere Produktivität nutzen – aber auch Risiken wie Cyberangriffe müssen gemanagt werden.
Industrie 4.0 ist mehr als nur ein teurer Hype – sie revolutioniert mit Vernetzung, KI und dem Internet of Things (IoT) die Industrielandschaft, steigert Produktivität und Flexibilisierung und schafft smarte Produktionsprozesse. Doch das Management muss Chancen und Risiken abwägen, denn ohne klare Strategie bleibt die digitale Transformation nur eine kostspielige Spielerei.
Starte mit einer klaren Digitalisierungsstrategie, die Ziele von Industrie 4.0 definiert – von Smart Factory bis selbststeuernde Produktionsprozesse. Nutze Industrial Internet of Things (IIoT), Maschinelles Lernen und den Digitalen Zwilling, um Montagelinien effizienter zu machen, während eine systemtechnische Verbindung für reibungslose Kommunikation sorgt.
Bestehende Maschinen müssen nicht immer ausgetauscht werden – dank Nachrüstlösungen wie Sensoren, IIoT-Modulen und Digitalen Zwillingen können selbst alte Fließbänder und Montagelinien smarter werden. So verbindet die Industrie 4.0 klassische Produktionsprozesse mit modernster Kommunikationstechnologie, Maschinellem Lernen und Selbststeuerung, um Effizienz, Flexibilität und Wettbewerbsfähigkeit zu steigern.